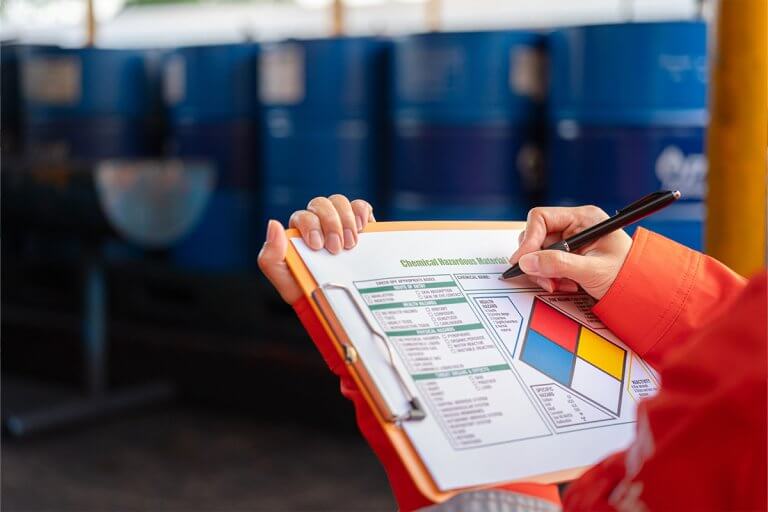
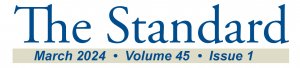
New Rule Boosts Chemical Facility Safety Standards to Protect Communities
On March 1, 2024, the U.S. Environmental Protection Agency (US EPA) announced the finalization of amendments to the Risk Management Program (RMP), marking a significant step forward in the protection of at-risk communities from chemical accidents. The initiative, dubbed the “Safer Communities by Chemical Accident Prevention Rule,” introduces the most protective safety provisions for chemical facilities in the agency’s history.
The final rule aims to bolster prevention, preparedness, and public transparency regarding chemical hazards. It mandates that industry sectors with high accident rates implement stronger safety measures to prevent accidental releases of hazardous chemicals. Such incidents are characterized by the US EPA as ones that can lead to fatalities, injuries, environmental damage, and necessitate emergency actions like evacuations or shelter-in-place orders.
US EPA Administrator Michael S. Regan emphasized the rule’s importance in advancing environmental justice, highlighting its potential to safeguard overburdened and underserved communities across the country. The rule was introduced first in 2017; rescinded and modified in 2019; published in 2022; and then released in its final state with amendments based on comments received on the 2022 version on March 1, 2024.
Key Provisions and Expected Impacts
Safer Technologies and Alternatives Analysis: Facilities are now required to conduct an analysis of safer technologies and alternatives. For some, this includes the implementation of reliable safeguard measures to mitigate accident risks such as requiring emergency back-up for perimeter monitors. US EPA is also collecting information during the plan submission process to better understand the technology being deployed in process and perimeter monitors to determine whether they meet the RAGAGEP* standard and are able to detect the compound being monitored as opposed to a surrogate.
- Worker Empowerment/Employee Participation: The rule advances employee participation in accident-prevention processes, including decision-making, training, and anonymous hazard reporting.
- Third-Party Audits: Facilities with a history of accidents must undergo third-party, independent compliance audits (NAICS code 324 and 325 facilities are subject to this change).
- Enhanced Emergency Preparedness: The amendments stress the need for timely information sharing with local responders and the establishment of community notification systems.
- Climate Risks Evaluation: Facilities must assess the risks posed by natural hazards and climate change, including power loss scenarios.
- Others: Other changes include enhanced regulation around facility siting, root-cause analysis, and making key RMP data available to the public.
* Recommended and Generally Accepted Good Engineering Practices
The “Safer Communities by Chemical Accident Prevention Rule” represents a culmination in the US EPA’s efforts to enhance chemical safety and public health protection by mandating stricter safety measures and promoting transparency. The rule is expected to decrease the frequency and severity of chemical accidents, thereby minimizing their impact on at-risk communities, and will be published alongside a query tool allowing people to access information for RMPs in nearby communities.
Ramifications for Industrial Operations
The final rule’s emphasis on safer technologies and alternatives analysis could prompt a shift in how facilities manage chemical processes. Industries may need to invest in new technologies or modify existing processes to meet the updated standards, potentially leading to significant operational changes. This could also drive innovation in chemical safety technologies and practices and require significant capital expenditures.
The requirement for worker participation in safety decisions underscores the value of a knowledgeable and engaged workforce in accident prevention. Facilities will be required to enhance training programs and develop systems for anonymous hazard reporting, ideally leading to improved overall safety culture and more administrative challenges to investigate possible disgruntled employee claims.
Increased independent reviews through mandatory third-party audits and detailed incident investigations, will likely lead to higher compliance costs for facilities. However, these measures are likely to result in long-term savings by preventing costly accidents and associated liabilities through the deployment of more qualified independent Auditors.
The focus on climate risks and emergency preparedness highlights the need for facilities to consider broader environmental factors in their risk management strategies. With the increased transparency to local communities through the reporting tool, we are likely to see an increase in environmental justice considerations. The hope is that this will encourage more sustainable operational practices and resilience planning.
Of note, the US EPA did not finalize compliance audit language at 40 CFR 68.58(a) and 68.79(a) which proposed auditing for every covered process at a facility. This corrected an error in the proposed rulemaking text. By not finalizing this language, compliance audits remain consistent with the current practice, which allows for representative sampling. A discussion of representative sampling as an acceptable practice for compliance audits can be found in the reconsideration final rule at 84 FR 69834 (69882), a portion of which is provided below:
… CCPS “Guidelines for Auditing Process Safety Management Systems, Second Edition” (Wiley, 2011), provides two methods for representative sampling that are designed to ensure a compliance audit at a medium to large multi-process facility represents all covered processes at the facility without sampling records or personnel for every prevention program provision at every covered process. The two methods offered by CCPS are to either (1) Audit some elements of the prevention program in all covered processes and units (CCPS provides an example indicating that different subsets of prevention elements are selected for different units, such that every element is ultimately audited under this approach), or (2) Audit all elements of the prevention program in some of the processes and units.
The Agency agrees that either of these approaches can produce an audit reflecting regulatory compliance for each RMP prevention program element at each covered process. However, where an owner or operator chooses to perform such a representative sampling approach, under either method (or a combination of both methods) they must demonstrate that the information audited is truly reflective of regulatory compliance for each process at the source. If the owner or operator can demonstrate that an audit of an accident prevention provision at one or more processes is representative of the owner’s compliance with the prevention provision at other processes at the source, then a source may use the review of that aspect in one process to address and evaluate other processes, so long as all prevention requirements are evaluated and addressed for all processes at the source either directly or by such representative testing every three years. All covered processes and units must be in the pool from which the representative sample is selected, and any findings of the audit must be addressed, and deficiencies corrected at all units. If a facility implements representative sampling to satisfy compliance audit requirements for multiple processes, the Agency will evaluate whether non-compliance with an RMP prevention program element is also evidence of inadequate compliance audit procedures …
Overall, while the final rule presents challenges for the affected industries, proactive adoption can help facilities to not only comply with regulations, but also take advantage of opportunities to enhance safety, environmental protection, and community relations, thereby increasing stakeholder value.